The Differences Between Pressure-Treated and Marine-Grade Plywood
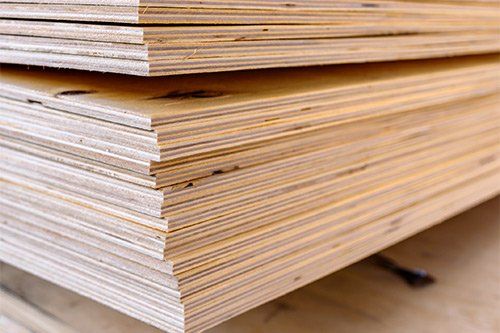
Better tools may make a project move along faster or easier, but it is the quality of the materials that determine the strength and appearance of the final product. Some projects do not need the strongest, most durable plywood, but others will fail quickly if the builders make incorrect plywood choices. Here is how to choose the plywood you need between pressure-treated and marine-grade plywood.
Use of Pressure-Treated Plywood
Pressure-treated plywood is chemically treated to prevent insect damage and to protect against rot, and it can survive outside without added protection if exposed only to average amounts of water like an occasional rainstorm or garden hose. Damage occurs with submersion of the wood in water or its use as an exterior material in very wet environments.
Manufacturers can apply a water-resistant finish that will reduce the risk of warping and rot when the plywood is in or on the water. The finish may extend the life of the material, but it is not a permanent solution. The problem is the voids in the wood caused by naturally occurring grooves and holes. Water can enter these voids and cause the wood to rot from the inside.
Another concern with submerging pressure-treated plywood is the risk of chemicals leaching into the water. In the past, the chemicals used to treat the wood were arsenic and copper. Arsenic can accumulate in the tissue of fish and other animals, and high levels of copper are toxic to marine life. Today, many brands of plywood still use copper, but not arsenic.
However, studies have been unable to produce any conclusive evidence that the level of the chemicals in the wood is enough to cause serious health risks to nearby marine life. So it is still legal to use pressuretreated plywood in docks and other structures in the water in Florida. Although, it is still not the most efficient material for this purpose.
A better type of use for basic pressure-treated plywood is in yards that are not overly wet or directly against waterways. Use pressure treated plywood to build decks, steps, and picnic tables. The wood is also safe for raised-bed gardens and children's playsets.
Use of Marine-Grade Plywood
Lamination under high heat and pressure and the use of waterproof glue helps to make marine grade plywood more durable for wet environments. The glue fills all the voids to keep each layer tight to prevent any warps or rot. Manufacturers also use hardwood for this product, so it is even more durable.
You can protect the wood even more and make it last much longer by painting a waterproof sealant painted on a plywood dock, boat, or other immersed object. The sealant can last much longer on marine plywood than on wood boards that do not undergo the same lamination process. Another benefit of using marine plywood is that it can reduce the amount of resealing the structure needs.
Marine-grade plywood does not undergo a chemical treatment to prevent decay like traditional pressuretreated products. The absence of the chemicals means it will not deposit hazardous materials into nearby waterways or into the water when immersed or submerged.
Many people use marine plywood for boats, docks, and other projects on or near the water or in other wet environments. The plywood can even help to prevent rot in spas, bathrooms, and other interior areas where dampness is common. In fact, marine-grade plywood will work effectively for any plywood project.
Reputable suppliers know the difference between marine-grade plywood and high grades of traditional pressure-treated plywood. At Mikro Corporation , our clients can trust the materials we supply for their projects because we understand the importance of every job. Contact us to learn more about our product line or to begin your order.